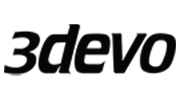
3Devo for University Research
Testing Without Limitations
Researchers at Embry-Riddle Aeronautical University have embarked on an ambitious project – creating a self-contained, cost-effective, 3D printable heat sink by combining phase-change materials with plastics. The Composer Filament Maker is taking them closer to making that vision a reality.
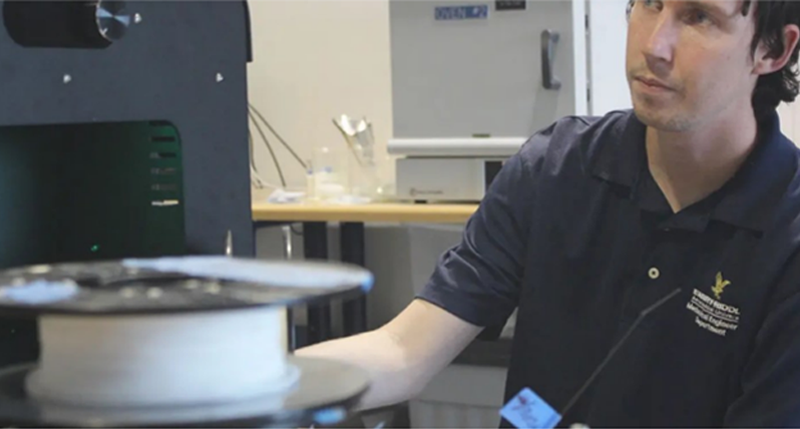
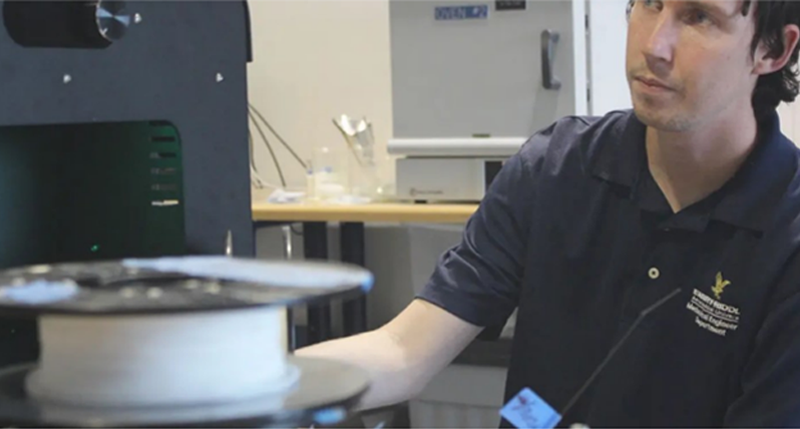
3Devo for University Research
Testing Without Limitations
Researchers at Embry-Riddle Aeronautical University have embarked on an ambitious project – creating a self-contained, cost-effective, 3D printable heat sink by combining phase-change materials with plastics. The Composer Filament Maker is taking them closer to making that vision a reality.
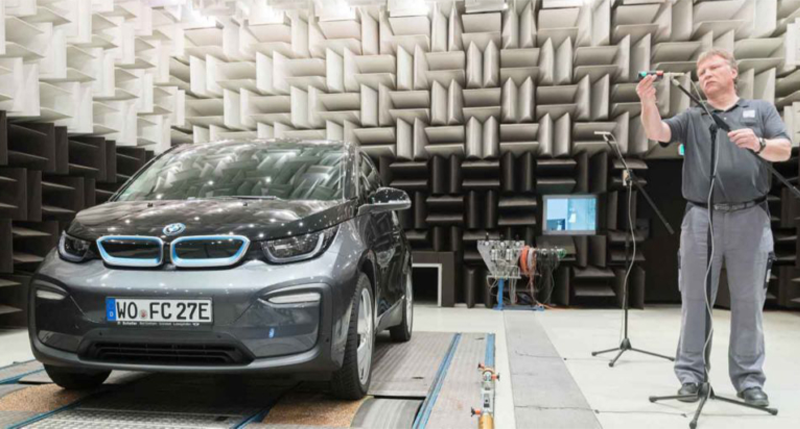
3Devo Sika Automotive Manufacturing
Maximizing efficiency, while reducing development times
Sika Automotive, a preferred partner for leading OEMs and automotive component suppliers, needed to streamline prototyping and pre-series production for their innovative heat-expandable acoustic inserts. 3devo’s Composer 350 Filament Maker, capable of extruding heat-reactive, low-temp materials, has helped Sika switch to in-house 3D printing.
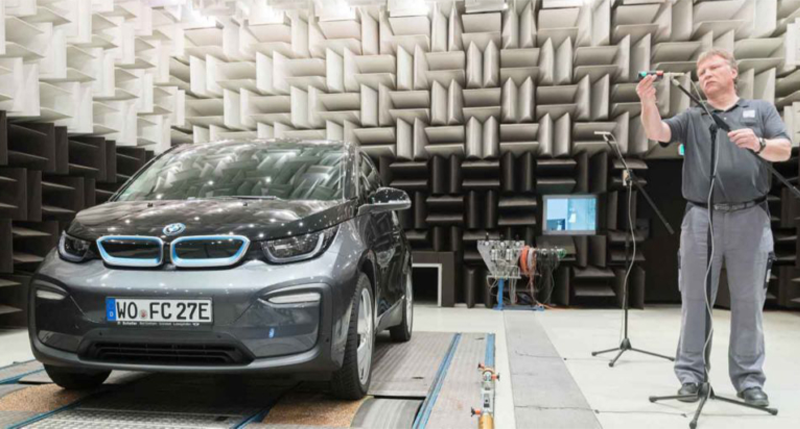
3Devo Sika Automotive Manufacturing
Maximizing efficiency, while reducing development times
Sika Automotive, a preferred partner for leading OEMs and automotive component suppliers, needed to streamline prototyping and pre-series production for their innovative heat-expandable acoustic inserts. 3devo’s Composer 350 Filament Maker, capable of extruding heat-reactive, low-temp materials, has helped Sika switch to in-house 3D printing.
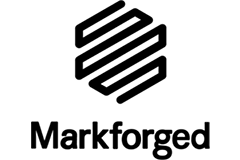
3D Printer Enables Toolmaker to Produce Fixturing, End-Use Parts
BETTER PRODUCTION ADDITIVE MANUFACTURING
Identifying and solving bottlenecks is an important part of keeping any business running. Elliott Tool Technologies iden tified a holdup in the process of producing its workholding fixtures, one that a 3D-printing system from Markforged (Cambridge, Massachusetts) has helped to solve
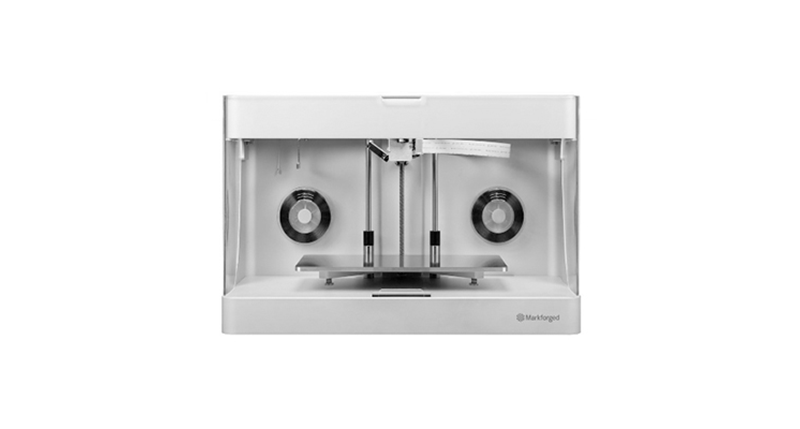
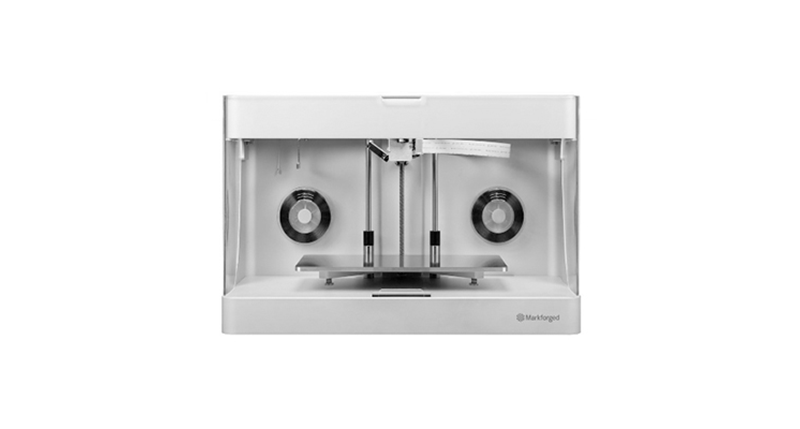
3D Printer Enables Toolmaker to Produce Fixturing, End-Use Parts
BETTER PRODUCTION ADDITIVE MANUFACTURING
Identifying and solving bottlenecks is an important part of keeping any business running. Elliott Tool Technologies iden tified a holdup in the process of producing its workholding fixtures, one that a 3D-printing system from Markforged (Cambridge, Massachusetts) has helped to solve
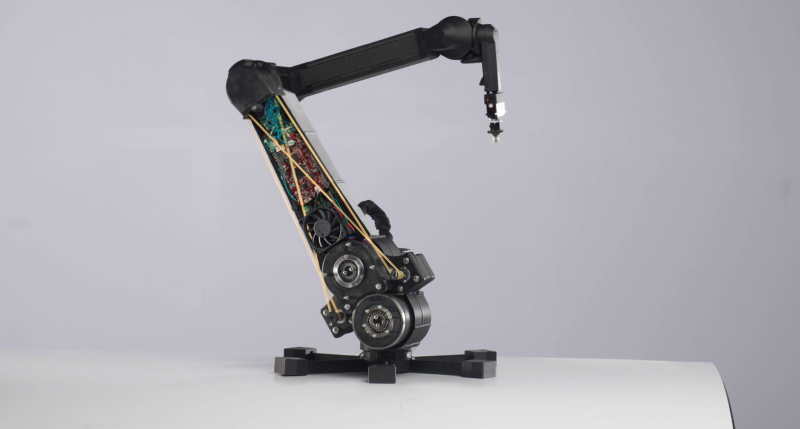
7-Axis Robotic Arm Case Study
End-Use Product
Dexter manufacturer Haddington Dynamics supplies its 7-axis fully assembled robotic arms and kits to NASA, GoogleX, and Toshiba. After using the arm, a high-profile customer suggested they move away from using weak PLA material and instead utilize Markforged’s Onyx material with continuous carbon fiber reinforcement to achieve the strength they desired.
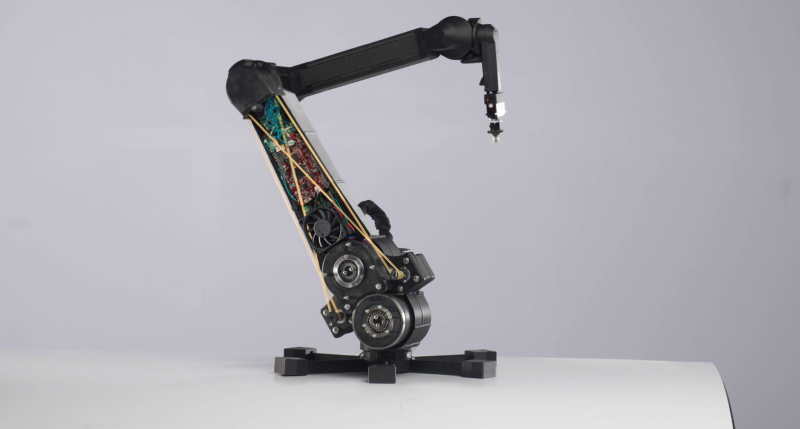
7-Axis Robotic Arm Case Study
End-Use Product
Dexter manufacturer Haddington Dynamics supplies its 7-axis fully assembled robotic arms and kits to NASA, GoogleX, and Toshiba. After using the arm, a high-profile customer suggested they move away from using weak PLA material and instead utilize Markforged’s Onyx material with continuous carbon fiber reinforcement to achieve the strength they desired.
Application Use Case - Dixon Gripper Metal
A Place for Metal
Dixon Valve has long used Markforged composite 3D printers to manufacture End of Arm Tooling (EOAT) for their many robotic arms. However, they could not print grippers that held abrasive surfaces. The threads these grippers hold quickly wear out printed composite parts, which while strong have the same surface hardness as thermoplastics. By printing the grippers with the Metal X, Dixon Valve achieves the same advantages that 3D printing affords without sacrificing part durability.
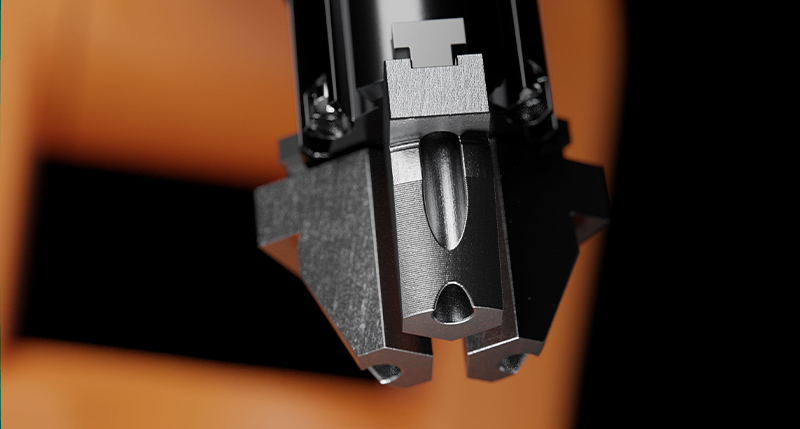
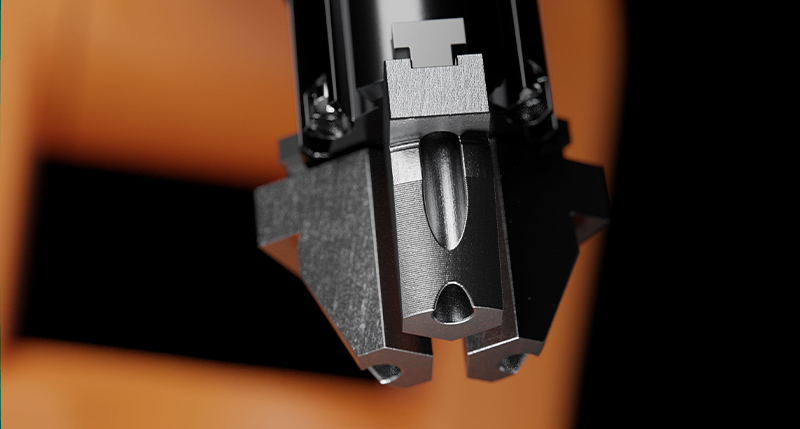
Application Use Case - Dixon Gripper Metal
A Place for Metal
Dixon Valve has long used Markforged composite 3D printers to manufacture End of Arm Tooling (EOAT) for their many robotic arms. However, they could not print grippers that held abrasive surfaces. The threads these grippers hold quickly wear out printed composite parts, which while strong have the same surface hardness as thermoplastics. By printing the grippers with the Metal X, Dixon Valve achieves the same advantages that 3D printing affords without sacrificing part durability.
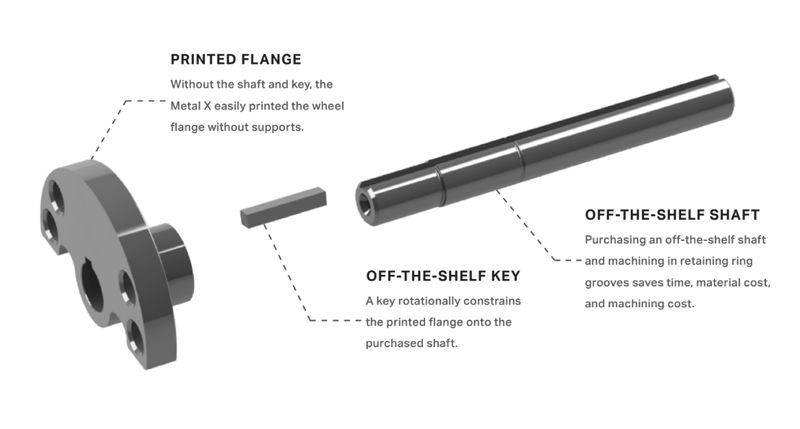
Application Use Case - Wheel Shaft
Efficient Fabrication
Stanley Infrastructure used to machine wheel shafts out of a single block of steel. Because of the diameter of the flange and the length of the shaft, this meant that ~90% of the stock material was wasted in each part. With the help of Markforged engineers, Stanley Infrastructure redesigned the wheel shaft to be a three-part assembly.
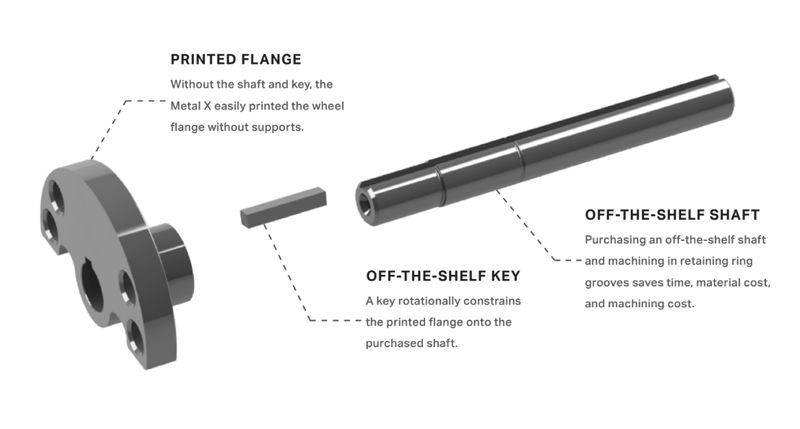
Application Use Case - Wheel Shaft
Efficient Fabrication
Stanley Infrastructure used to machine wheel shafts out of a single block of steel. Because of the diameter of the flange and the length of the shaft, this meant that ~90% of the stock material was wasted in each part. With the help of Markforged engineers, Stanley Infrastructure redesigned the wheel shaft to be a three-part assembly.
Case Study - Dixon Valve & Coupling - Print Version
As soon as Dixon Valve unboxed their industrial strength Markforged 3D printer, they put it to work. “We were able to re-tool a robotic arm in a manufacturing cell in under 24 hours,” Everett exclaimed.
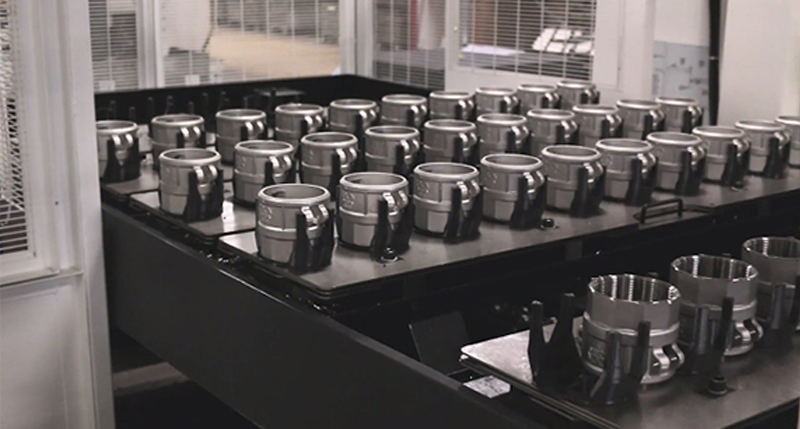
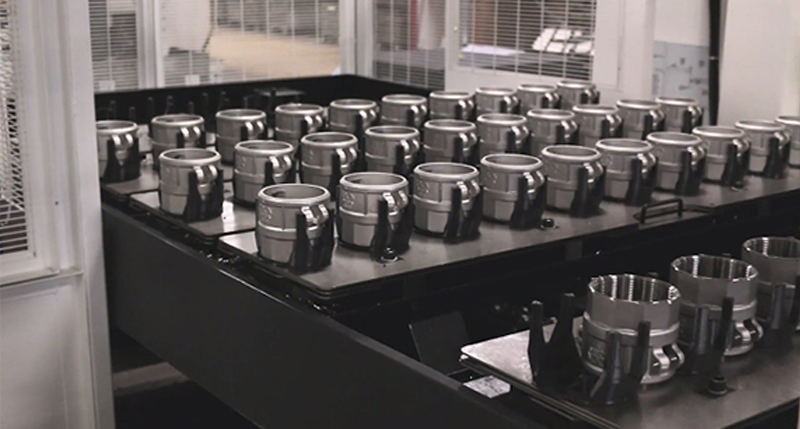
Case Study - Dixon Valve & Coupling - Print Version
As soon as Dixon Valve unboxed their industrial strength Markforged 3D printer, they put it to work. “We were able to re-tool a robotic arm in a manufacturing cell in under 24 hours,” Everett exclaimed.
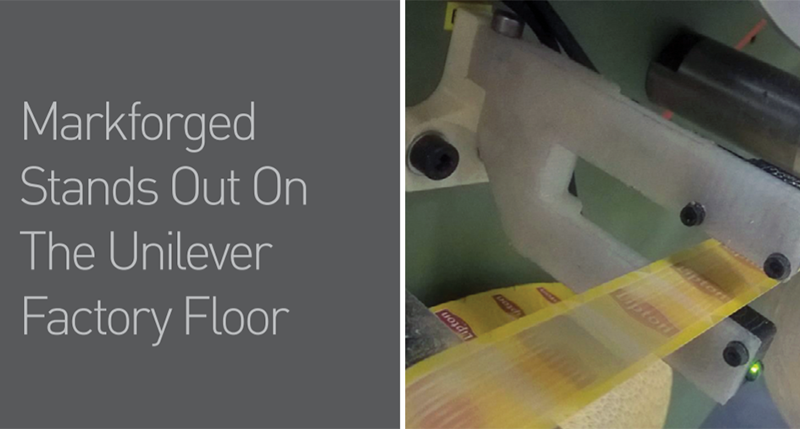
Case Study - Unilever
Markforged Stands Out On The Unilever Factory Floor
These parts are developed very quickly, and it’s about one night to print a few parts for the machine. They are much stronger and more durable than any parts printed on a normal 3D printer.
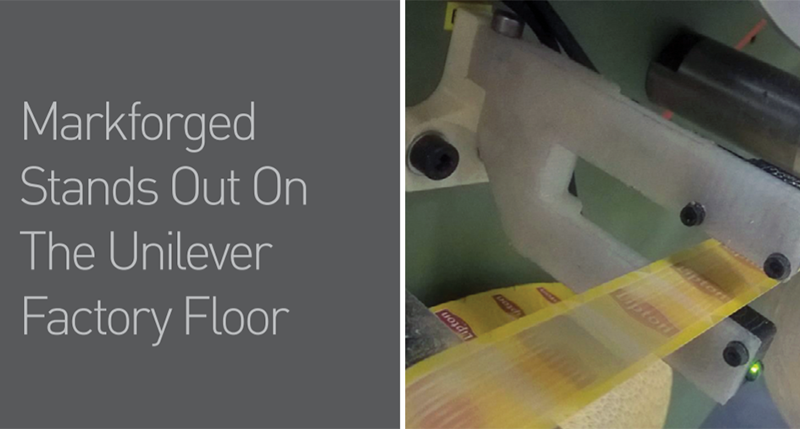
Case Study - Unilever
Markforged Stands Out On The Unilever Factory Floor
These parts are developed very quickly, and it’s about one night to print a few parts for the machine. They are much stronger and more durable than any parts printed on a normal 3D printer.