What are the Different Types of 3D Printing Methods?
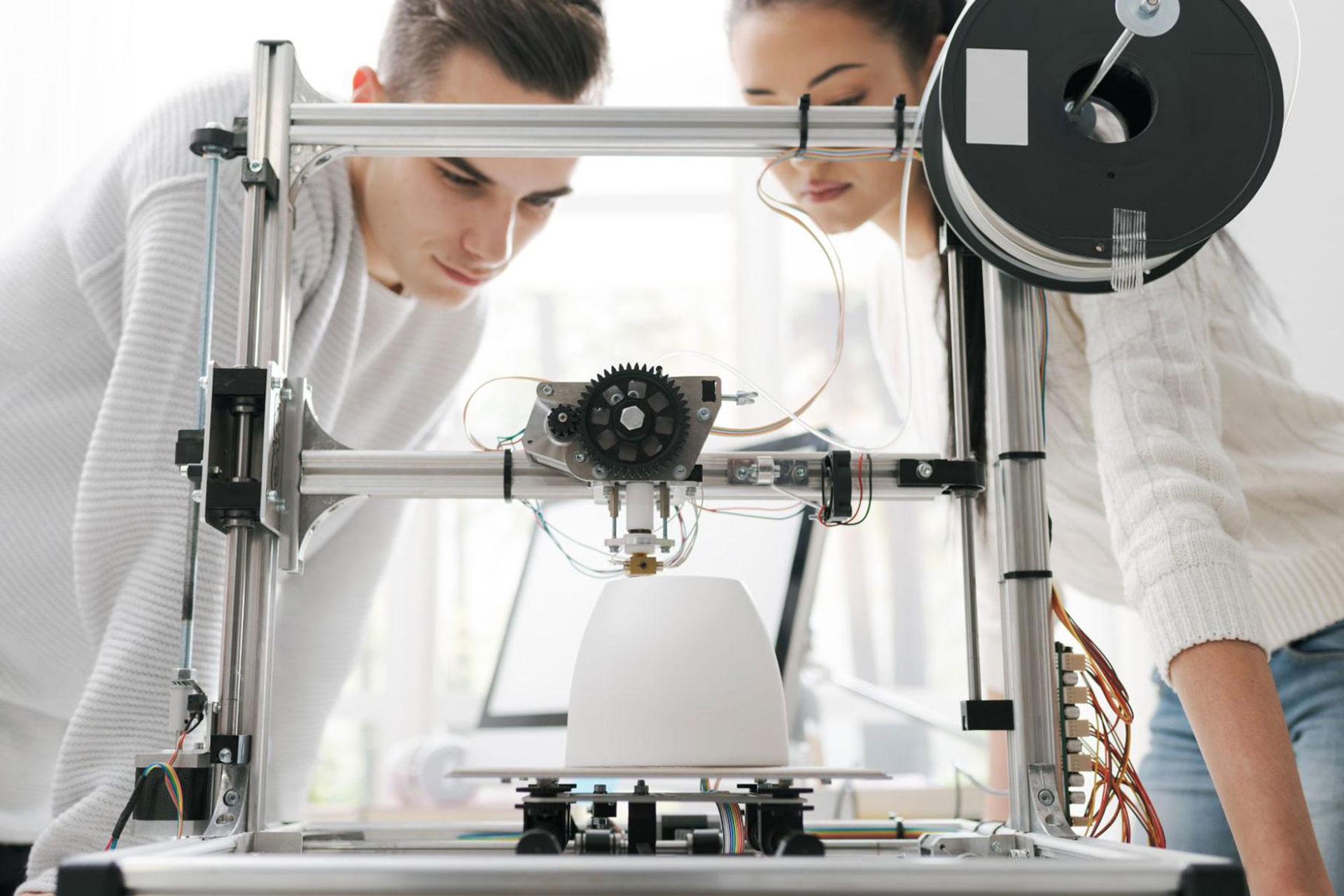
Also known as additive manufacturing, 3D printing is a technology that creates objects layer by layer instead of the usual way of manufacturing them from solid block material. Since every structure or object manufactured varies in terms of the materials used, the 3D printing method also varies, and each one is made suitable for forming materials such as plastic and metal. To be able to create these parts, the process would involve different types of 3D printing methods.
1. Digital Light Process (DLP)
Digital Light Process or DLP is a 3D printing method that works with photopolymers just like SLA (stereolithography). DLP on the other hand, prints faster than SLA and makes use of a light projector screen, while SLA uses UV laser. Manufacturing parts will not be a problem for 3D printers who use DLP because this method can create an entire layer straight away, making it ideal if you require a faster building speed. Parts created using DLP have smooth and refined surface areas. This 3D printing method is also able to create complex designs and geometries, making it a common choice for applications such as jewelry, decorative arts, and prototyping.
A downside to DLP, however, is that objects or parts created using this method easily debase when left out in the sun. While DLP performs well in terms of printing speed, it can also come out more expensive than other printing methods such as FDM. This is for the reason that DLP uses resins instead of filaments, and resins are more expensive.
2. Direct Metal Laser Sintering (DMLS)
Direct Metal Laser Sintering (DMLS) is a 3D printing process that uses a laser instead of a plastic filament to fuse fine metallic powders into complex parts. This method, which is also known as direct metal laser melting (DMLM), is similar to selective laser melting (SLM), and uses steel powder to create objects that are stronger than plastic versions, as well as objects composed of alloys with different melting points.
3. Electron Beam Melting (EBM)
The Electron Beam Melting (EBM) process uses a high-power electron beam to melt the powder, which is then used to produce parts. The hot process and vacuum created inside the chamber allow you to produce parts with no residual stress. While using EBM, it is possible to produce high-quality parts that are economically viable, have a more homogenous composition, and improved mechanical properties.
4. Fused Deposition Modeling (FDM)
Fused Deposition Modeling, or FDM 3D Printing for short, is one of the most basic forms of additive manufacturing. It’s a process where you start with a spool of raw material, typically ABS plastic or something similar, and then feed that raw material into a machine to be heated in its glass transition temperature. With this very low melting point, the plastic cools as it leaves the nozzle and rapidly cools onto a layer or platform below, forming a part of the object being printed. By controlling how quickly this happens, each layer can be created as thin or thick as you want it.
5. Laminated Object Manufacturing (LOM)
Laminated Object Manufacturing (LOM) is a process that creates three-dimensional objects from a stack of thin sheet materials using heat and pressure as the only means of joining them. The most common materials used for this type of manufacturing are paper, plastic, and metal. To create an object using LOM, you begin by cutting stacks of sheets into flat, narrow strips. You then lay one strip on top of another and glue them together at the edges. You then stack these joined strips on top of one another to form a 3D object. This method takes on many different names depending on the specific material being used — paper laminate, plastic laminate, metal laminate, etc.
6. Stereolithography (SLA)
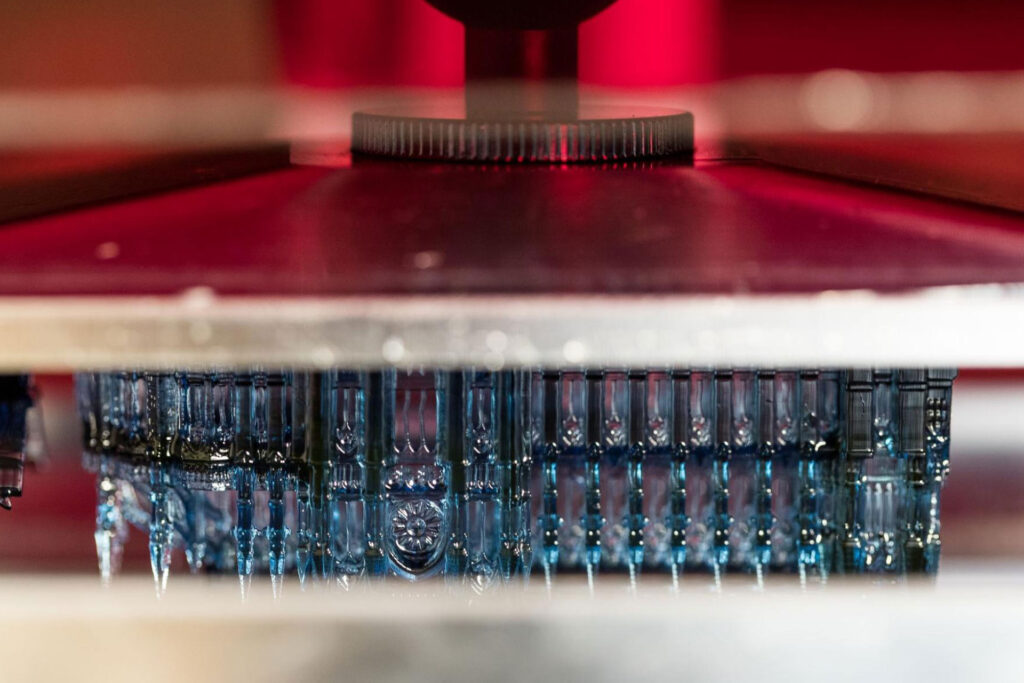
The Stereolithography (SLA) method starts by making a copy of the support structures, and then it makes the part itself. It does this by pointing an ultraviolet laser at a kind of liquid plastic resin, which hardens when exposed to UV light. The UV laser draws each layer on the surface of the resin, one at a time. After each layer is drawn onto the resin, the platform holding your part moves down and a bar moves along it to put on another layer of resin. This process is repeated over and over until your part is complete.
7. Selective Laser Sintering (SLS)
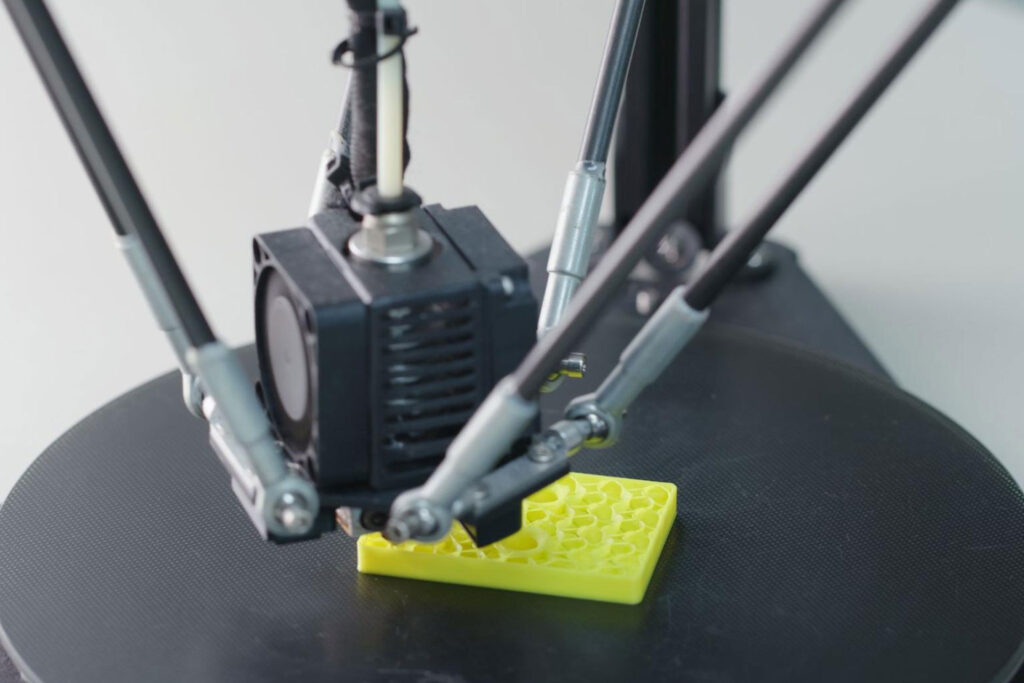
Objects created with Selective Laser Sintering (SLS) are made with powder materials, such as nylon. A computer tells a laser what object to print, which traces over the cross-section of that object onto the powder. The laser then heats up the powder just below or above its boiling point, causing the particles to fuse together into a solid form.
8. Selective Laser Melting (SLM)
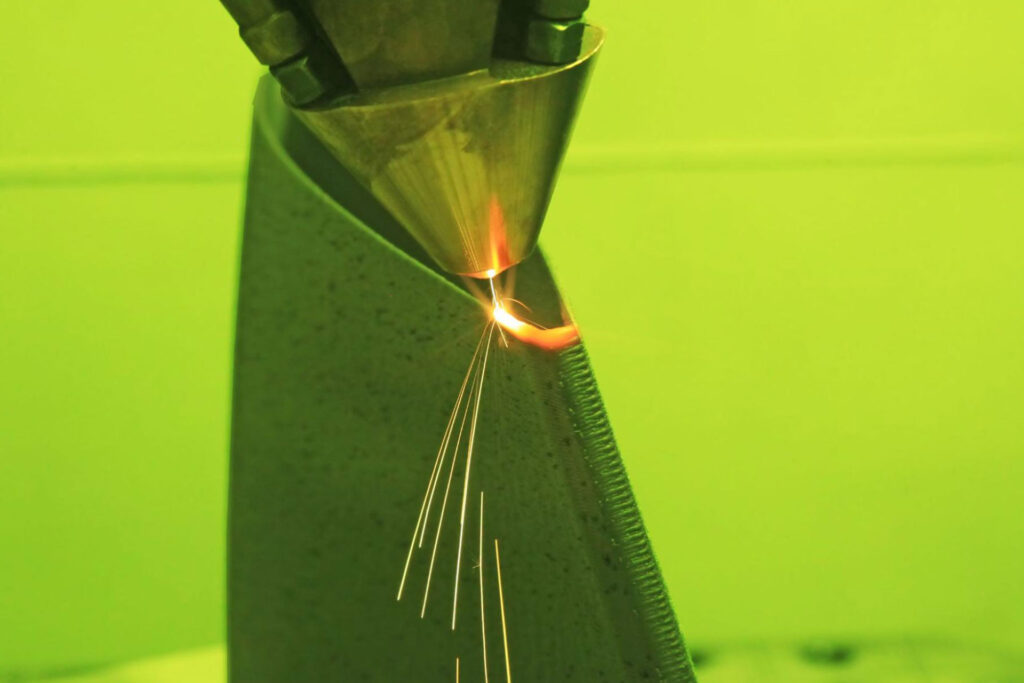
Selective Laser Melting (SLM) is a high-energy process because the metal powder must be heated above its melting point. Stresses and dislocations can occur during the process, which can impact the final product’s properties. The difference between SLM and DMLS is that SLM heats metal powder until it fully melts into a liquid. DMLS fuses metal powder to form a solid, but it does not melt the metal, so less energy is needed. Sintering heats particles enough so that their surfaces join together.
Looking for quality 3D printing in the Philippines? Contact us today to know more about our products!