10 Design Tips for Successful SLA 3D Printing
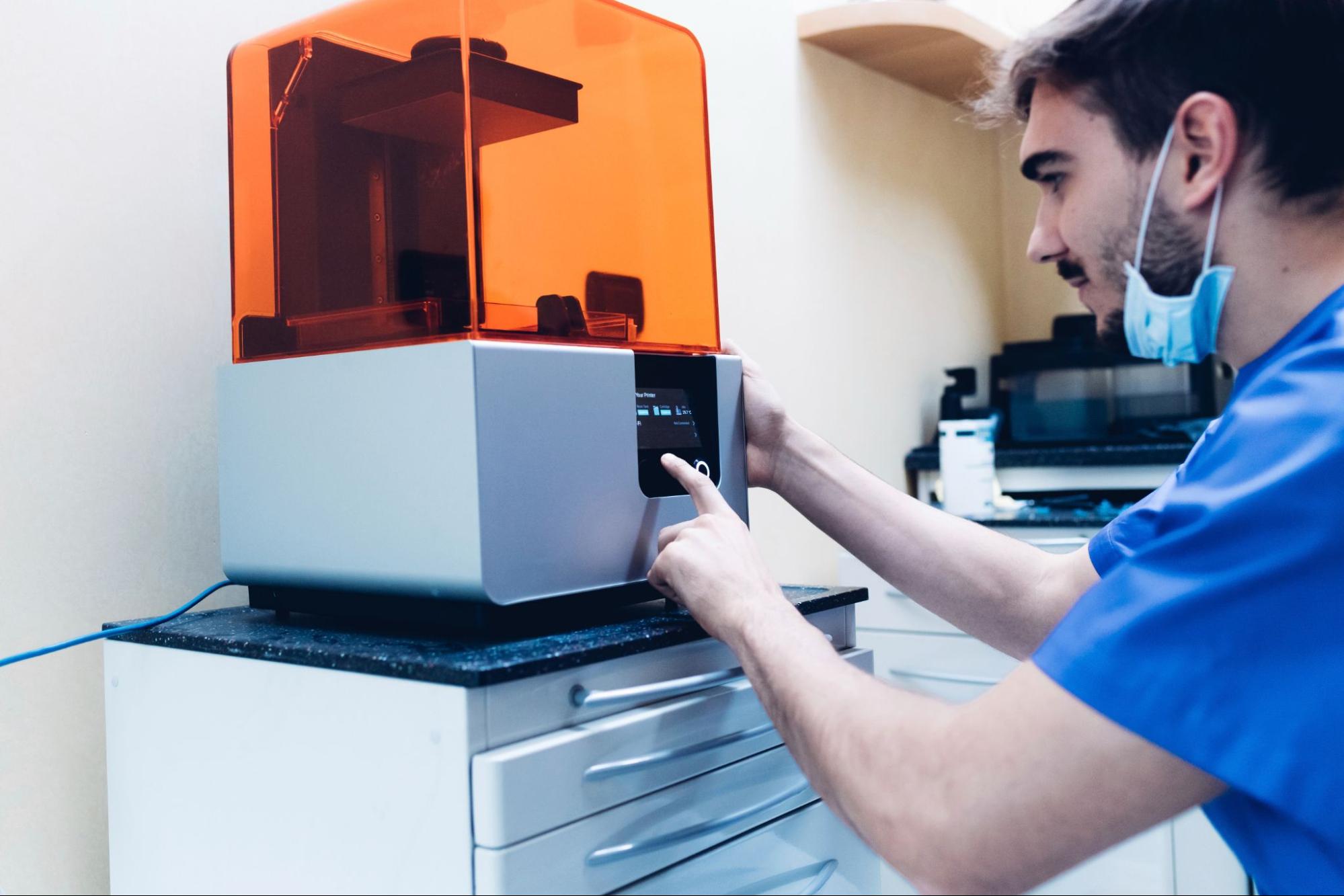
Stereolithography (SLA) 3D printing is renowned for its high precision, smooth surface finishes, and the ability to create intricate details that other 3D printing methods might struggle with. However, achieving successful SLA prints requires a good understanding of the design process and specific considerations unique to this technology. Whether you’re a beginner or looking to improve your print quality, these design tips will help you get the most out of your SLA 3D printer.
Related: What is Stereolithography (SLA)? Understanding the Basics of Resin 3D Printing
On This Page
- Know Your Material Options
- Optimize Your Design for SLA Printing
- Design for Printability
- Streamline for Post-Processing
- Test and Iterate
- Manage Resin Handling and Maintenance
- Optimize Print Settings for Better Results
- Utilize SLA Software Features
- Maintain Your SLA Printer
- Consider Environmental Factors
1. Know Your Material Options
SLA printing offers a variety of resins, each with its own properties. Some resins are flexible, others are strong, heat-resistant, or highly detailed. Choosing the right resin for your project is key to ensuring a successful print.
Standard Resins
Most common type of resin used for SLA 3D printing. It offers a smooth surface and fine details, making it ideal for general use and popular across various applications due to its excellent mechanical properties.
Tough Resins
Ideal for parts that need to withstand stress or impact, including functional prototypes and industrial applications that need durability.
Flexible Resins
Suitable for soft, pliable parts that can bend without breaking. These resins are often used in applications requiring elastic or rubber-like qualities.
High-Temperature Resins
Best for parts that will be exposed to high heat, as they are built to handle high temperatures and stay strong, which is essential for industrial use.
Understanding the properties of each resin type will help you select the right one for your application, which is critical for achieving the desired performance and appearance.
2. Optimize Your Design for SLA Printing
Mind the Wall Thickness
Wall thickness is a crucial factor in SLA design. Too thin, and your parts may be fragile or fail during printing. Too thick, and you might waste material or have issues with warping.
- Recommended Wall Thickness: For unsupported walls, the minimum recommended thickness is 0.6 mm. But for walls with support on both sides, a thickness of 0.4 mm is sufficient, as they are less prone to warping.
Consider Part Orientation
The orientation of your part on the build platform significantly affects print quality, strength, and the amount of support needed. Proper orientation can also minimize the appearance of layer lines and reduce post-processing efforts.
- Minimize Overhangs: Position parts to reduce overhangs that require supports.
- Avoid Large Flat Surfaces Parallel to the Build Platform: These can cause suction forces that may lead to print failures.
- Angle Parts Slightly: Angling your part about 30-45 degrees can help with adhesion and reduce layer lines.
Add Adequate Supports
Supports are necessary in SLA printing to prevent parts from deforming during the print. However, too many supports can cause marks on the surface, while too few can lead to print failure.
- Strategic Support Placement: Place supports at overhangs, bridges, and any areas that might sag without them.
- Reduce Contact Points: Use smaller touchpoints for support to make post-processing easier and reduce marks on the finished part.
3. Design for Printability
Account for Tolerances and Clearances
SLA printing can achieve very high precision, but it’s still essential to account for tolerances, especially when designing parts that will fit together.
- Clearances for Moving Parts: Leave at least 0.2-0.4 mm clearance between moving parts to ensure they function properly.
- Adjust for Post-Curing: SLA parts continue to cure and shrink slightly after printing, so factor this into your design, especially for tight tolerances.
Include Drainage Holes for Hollow Parts
When designing hollow parts, add drainage holes so uncured resin can escape. Without these holes, trapped resin can cause pressure, deform the part, or lead to print failures.
- Size and Placement of Holes: Make holes large enough to allow resin flow (typically 2-5 mm in diameter) and place them at the lowest points of your design.
4. Streamline for Post-Processing
Plan for Post-Curing
SLA prints require post-curing under UV light to reach their final material properties. Your design should accommodate this step, especially if you’re working with parts that have intricate details or fine features.
- Uniform Wall Thickness: Helps ensure even curing and reduces the risk of warping.
- Avoid Sharp Corners: Rounded edges cure more evenly and reduce stress concentrations that can cause cracks.
Sanding and Finishing
One of the benefits of SLA printing is the smooth surface finish it produces, but post-processing like sanding or painting may still be required.
- Minimize Support Marks: Use design software to adjust support placement or add features that will be sanded away.
- Layer Line Reduction: Orient parts to reduce visible layer lines and make sanding easier.
5. Test and Iterate
Prototype Before Final Print
It’s always a good idea to prototype your design before committing to a final print. A test print can reveal design flaws, tolerance issues, or areas that require additional support.
- Scale Down: Print a smaller version to save on time and materials while testing fit and functionality.
- Iterate Based on Results: Use the findings from your prototype to refine your design and improve the final product.
Use Print Settings to Your Advantage
Print settings such as layer height, exposure time, and print speed can significantly affect your print quality. Experiment with these settings to find the optimal balance for your specific design and material.
- Layer Height: Lower layer heights result in finer details but increase print time.
- Exposure Time: Proper exposure ensures the resin cures correctly without over-curing and affecting details.
6. Manage Resin Handling and Maintenance
Proper Resin Storage
Resin is sensitive to light and can degrade if not stored properly. Keep your resin in a cool, dark place, ideally in its original, opaque container with the lid tightly sealed to prevent exposure to light and air.
- Avoid Direct Sunlight: Store resin away from windows or other sources of UV light.
- Monitor Expiration Dates: Use fresh resin to avoid print defects related to expired or degraded materials.
Resin Reuse and Filtering
Resin can often be reused, but it’s essential to filter it before pouring it back into the bottle to remove any solidified particles that can affect print quality.
- Use a Fine Mesh Filter: Strain resin through a mesh filter after each print to catch cured particles or debris.
- Mix Resin Thoroughly: Shake or stir the resin well before each use to ensure the pigments and chemicals are evenly distributed.
7. Optimize Print Settings for Better Results
Adjust Layer Exposure Time
Layer exposure time significantly impacts print quality. While default settings often work, fine-tuning exposure can lead to crisper details and better print consistency.
- Reduce Overexposure: Overexposure can cause parts to swell and lose detail. Slightly reducing exposure time can sharpen details, especially for small or intricate parts.
- Test Exposure Levels: Use calibration prints like exposure test models to dial in the perfect exposure time for your resin and specific part features.
Fine-Tune Support Density and Touchpoint Size
Balancing support density and touchpoint size is crucial for successful prints. If supports are too dense, they’re hard to remove; if too sparse, your part might fail.
- Optimize Touchpoint Size: Smaller touchpoints leave fewer marks but may need to be denser. Larger touchpoints are stronger but more challenging to clean up.
- Adjust Density by Part Needs: Increase density for heavy or large parts and reduce it for delicate or small sections.
8. Utilize SLA Software Features
Use Advanced Features in Slicing Software
Modern SLA slicing software offers advanced features that can greatly improve your printing experience and outcomes.
- Adaptive Layer Heights: Adjust layer height dynamically based on the complexity of the part to save time without compromising detail where it’s needed most.
- Hollowing and Internal Supports: Use hollowing features to reduce resin usage and weight, and add internal supports to strengthen hollow parts without using excessive material.
Simulate Prints Before Printing
Many SLA slicing software options provide a simulation feature to preview how your part will be printed. This tool can help you identify potential issues like unsupported areas, stress points, or excessive suction forces.
- Preview Layer by Layer: Review each layer to ensure there are no surprises during printing.
- Check for Potential Failures: Look for red flags like unsupported overhangs or excessive stress areas that might need additional support.
9. Maintain Your SLA Printer
Regular Cleaning and Calibration
Keeping your SLA printer well-maintained is essential for consistent print quality.
- Clean the Vat: Regularly clean the resin vat to prevent cured resin remnants from affecting new prints.
- Check the Build Plate: Ensure the build plate is clean and properly leveled before each print to avoid adhesion issues.
- Inspect the Optics: Dust or smudges on the laser’s mirrors or glass can reduce print quality. Clean them carefully with a microfiber cloth if needed.
Replace Consumables as Needed
SLA printers have consumable parts like resin tanks, FEP films, and sometimes laser components that wear out over time.
- Monitor FEP Film Wear: A worn-out FEP film can cause adhesion issues or defects in prints. Replace it when you notice signs of wear like cloudiness or scratches.
- Check Resin Tank Condition: Resin tanks can degrade, especially with frequent use of harsh resins. Replace tanks when they show signs of wear to maintain print quality.
10. Consider Environmental Factors
Control Print Environment
Environmental factors such as temperature, humidity, and even light exposure can impact SLA printing.
- Temperature: Keep your printing environment at a consistent temperature (typically between 20-25°C or 68-77°F) for optimal resin curing.
- Humidity: High humidity can interfere with the curing process. Aim for a dry environment, ideally below 50% humidity, to avoid issues.
- Light Control: Minimize ambient UV light exposure to the printer and resin to prevent unintended curing.
Ventilation and Safety
SLA resins can emit fumes during the printing and curing processes. Proper ventilation and safety precautions are important.
- Ventilation: Ensure your workspace is well-ventilated to avoid inhaling fumes. Some printers come with built-in air filters or can be placed in ventilated enclosures.
- Personal Protective Equipment (PPE): Wear gloves when handling resin and isopropyl alcohol (used for cleaning prints) and consider eye protection when working with uncured resin.
Successful SLA 3D printing hinges on thoughtful design, careful material selection, and strategic print settings. Testing and iteration are crucial—don’t hesitate to adjust and refine your designs for the best results. We hope these tips help you master SLA 3D printing!
Looking for quality 3D printing in the Philippines? Contact us today to learn more about our products!