CNC Milling vs. CNC Grinding: Key Differences in Tools, Types and Applications
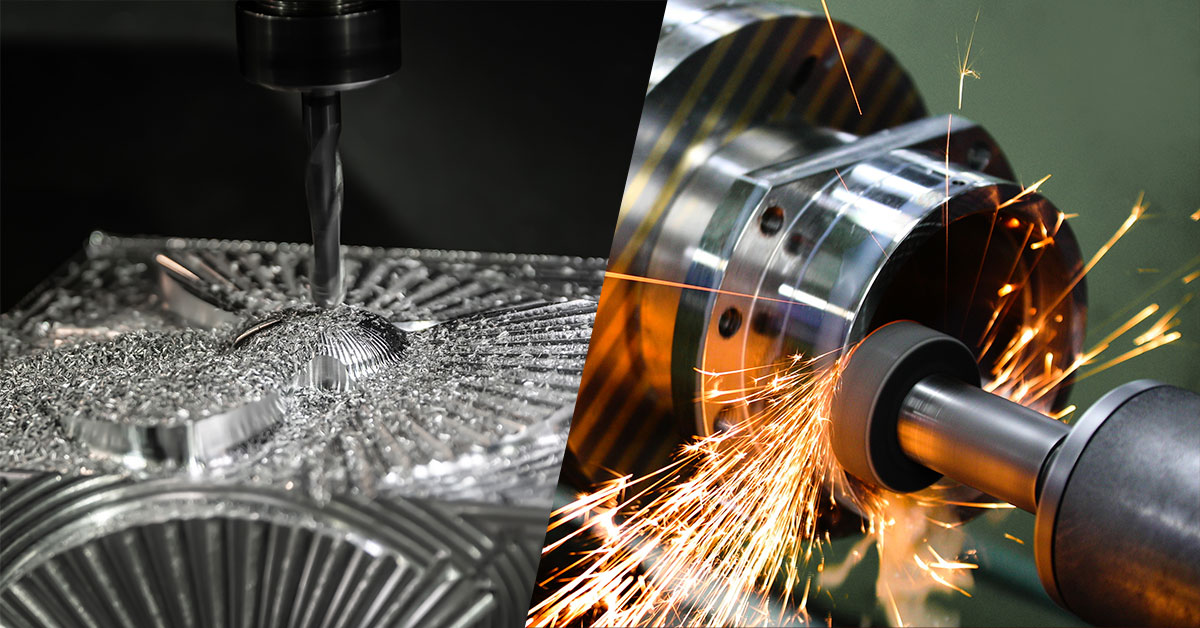
When it comes to precision manufacturing, two commonly used methods are CNC milling and CNC grinding. Both processes play an essential role in shaping materials, but they work in distinct ways. If you’re working in machining or just curious about these processes, understanding their differences is crucial as it enables you to know which one will work better with your project.
In this article, we’ll take a look at CNC milling and CNC grinding, comparing their tools, techniques, and applications to help you decide which is right for your project.
On This Page
- What is CNC Milling?
- What is CNC Grinding?
- Key Differences Between CNC Milling and CNC Grinding
- When to Choose CNC Milling vs. CNC Grinding
What is CNC Milling?
CNC milling is a machining process where rotary cutters remove material from a workpiece. It uses a computer-controlled machine to guide the movement of the cutting tool, allowing for precise control over the final shape and dimensions of the part.
Related: A Guide to What CNC Milling is All About
Tools Used in CNC Milling
The rotating cutter is a key component of CNC milling machines, which can have various shapes and sizes depending on the material being worked on and the type of cut required. Some common cutters include:
- End mills: Versatile tools that are typically used for the end milling process.
- Face mills: Used for cutting large, flat surfaces, as well as smoothing the surface.
- Drills: For creating holes in the material.
- Ball nose mills: Ideal for sculpting and creating curved surfaces.
CNC milling machines are versatile and can work with many materials like metals, plastics, and composites. The cutter moves along multiple axes while the material is fed in, allowing for detailed shapes, making CNC milling essential for precise manufacturing.
Types of CNC Milling
CNC milling uses different techniques based on the job at hand. Below are some of the types of milling:
- Face Milling: This technique involves using a cutter to remove material from a flat surface to create a smooth finish.
- Slot Milling: This method is used to create narrow channels or slots in a material.
Each technique is designed to handle different tasks, from basic cuts to intricate designs.
Applications of CNC Milling
CNC milling is ideal for projects that require high precision and complex shapes. Some common applications include:
- Aerospace parts: CNC milling is used to create intricate and lightweight components for aircraft.
- Medical devices: Precision milling ensures that medical tools and implants are made to exact specifications.
- Automotive components: From engine parts to body panels, CNC milling helps create strong and durable components.
Because of its flexibility, CNC milling can be applied to a wide range of industries.
What is CNC Grinding?
CNC grinding, on the other hand, focuses on using an abrasive wheel to remove material from a workpiece. Unlike milling, which relies on rotating cutters, grinding uses a wheel that spins at high speeds to finish surfaces to an extremely fine tolerance.
Related: What is CNC Surface Grinding? An Easy Guide
Tools Used in CNC Grinding
The main tool in CNC grinding is the grinding wheel as it is responsible for removing the primary material through its abrasive properties, which comes in various types to suit different materials and tasks. Some popular types include:
- Surface grinding wheels: Used for finishing flat surfaces.
- Cylindrical grinding wheels: Ideal for grinding round workpieces.
- Centerless grinding wheels: These are used when precision in the diameter of round parts is essential.
Grinding wheels come in a variety of grit sizes and hardness levels, depending on the material being worked on and the desired finish.
Types of CNC Grinding
CNC grinding is often used for tasks that require a fine finish or precise dimensioning. Common types include:
- Surface grinding: This is the most common type of CNC grinding, used to create smooth, flat surfaces.
- Cylindrical grinding: This process is used to grind the outside diameter of cylindrical parts, creating a smooth surface.
Applications of CNC Grinding
CNC grinding is typically used for applications that require an extremely fine finish or tight tolerances. Here are a few common uses:
- Tool sharpening: CNC grinding is used to sharpen tools like drills, milling cutters, and lathe tools.
- Precision components: Many industries, like aerospace and automotive, require parts to be made to exact dimensions and tolerances, which is where CNC grinding excels.
- Medical instruments: For fine finishes on surgical tools with complex forms and other high-precision instruments.
Grinding is often the choice when surface finish quality and dimensional accuracy are of paramount importance.
Key Differences Between CNC Milling and CNC Grinding
Now that we’ve covered the basics of both CNC milling and CNC grinding, let’s highlight the key differences between these two processes.
1. Tooling
- CNC Milling: Uses rotary cutters that remove material as they move across the workpiece.
- CNC Grinding: Uses an abrasive grinding wheel to wear down the material into a smooth finish.
2. Material Removal Method
- CNC Milling: Material is removed through cutting.
- CNC Grinding: Material is removed through abrasion.
3. Precision
- CNC Milling: Provides high precision, but typically not to the same level as grinding.
- CNC Grinding: Known for its ability to achieve ultra-fine tolerances and smooth surfaces.
4. Surface Finish
- CNC Milling: While it can achieve smooth finishes, it’s usually not as fine as those produced by grinding.
- CNC Grinding: Provides superior surface finishes and is ideal for applications that require a very fine, polished surface.
5. Speed and Efficiency
- CNC Milling: Generally faster for material removal, especially on larger parts.
- CNC Grinding: Can be slower, particularly for tougher materials, but it offers exceptional accuracy.
When to Choose CNC Milling vs. CNC Grinding
Understanding when to use CNC milling or CNC grinding depends on the specific needs of your project. Each process excels in different scenarios, so carefully consider the following:
Choose CNC Milling When:
- You need to remove large amounts of material quickly. Milling is designed for efficiency in material removal, making it ideal for roughing out shapes or preparing parts for final finishing.
- The project includes complex shapes, like detailed designs, slots, or holes. Milling tools are versatile, making it easy to create these features.
- Precision tolerances are important, but ultra-fine accuracy isn’t critical. Milling is perfect for applications that don’t demand polished surfaces or extreme dimensional precision.
Choose CNC Grinding When:
- The part requires an extremely smooth finish or tight dimensional tolerances. Grinding achieves exceptional surface quality and can work to tolerances as tight as 0.001 mm.
- You’re working with hard materials like hardened steel, ceramics, or carbide. It’s abrasive process is well-suited to handle tough materials.
- Surface smoothness is critical. Grinding is often chosen for components where roughness or imperfections could affect performance, such as bearings or cutting tools.
CNC milling and CNC grinding are both essential tools in modern manufacturing, each serving specific purposes and offering unique advantages. CNC milling is more versatile and efficient for shaping materials, while CNC grinding excels in achieving high-precision finishes. Learning more about their key differences in tools, techniques, and applications can help you determine which process is right for your specific needs.
So choose wisely, and you’ll ensure that your project meets its exact specifications with ease.
Looking for quality CNC Milling and CNC Surface Grinding in the Philippines? Contact us today to know more about our products!