A Guide to What CNC Milling is All About
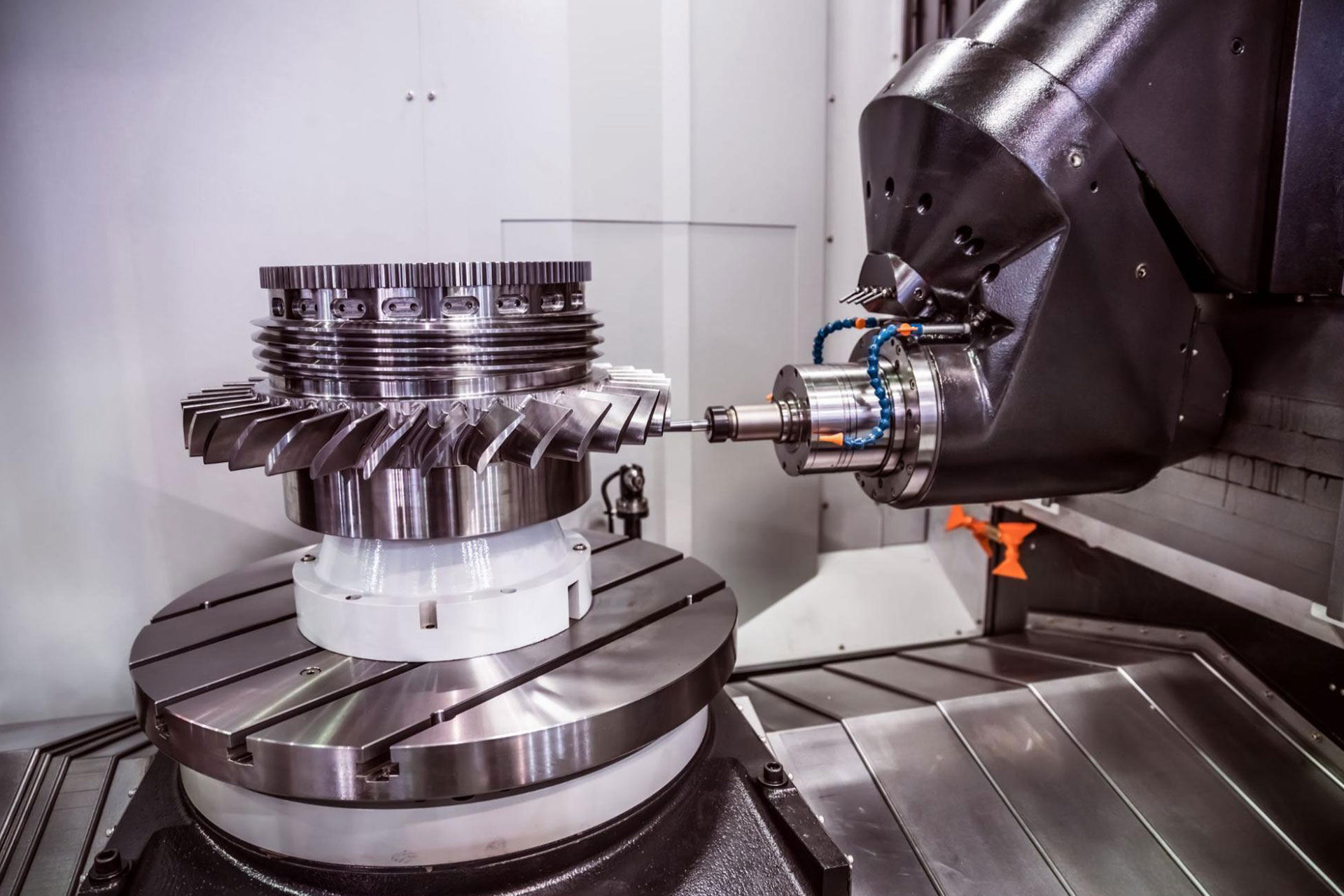
Before getting into the technical aspects, we’ll explain CNC milling. Regarding manufacturing, no other process is quite as versatile as CNC milling. Whether you need to fabricate mechanical parts for applications such as aerospace, automotive, and more or create a prototype that closely resembles the final product — CNC milling will get the job done.
What is a CNC Milling Machine?
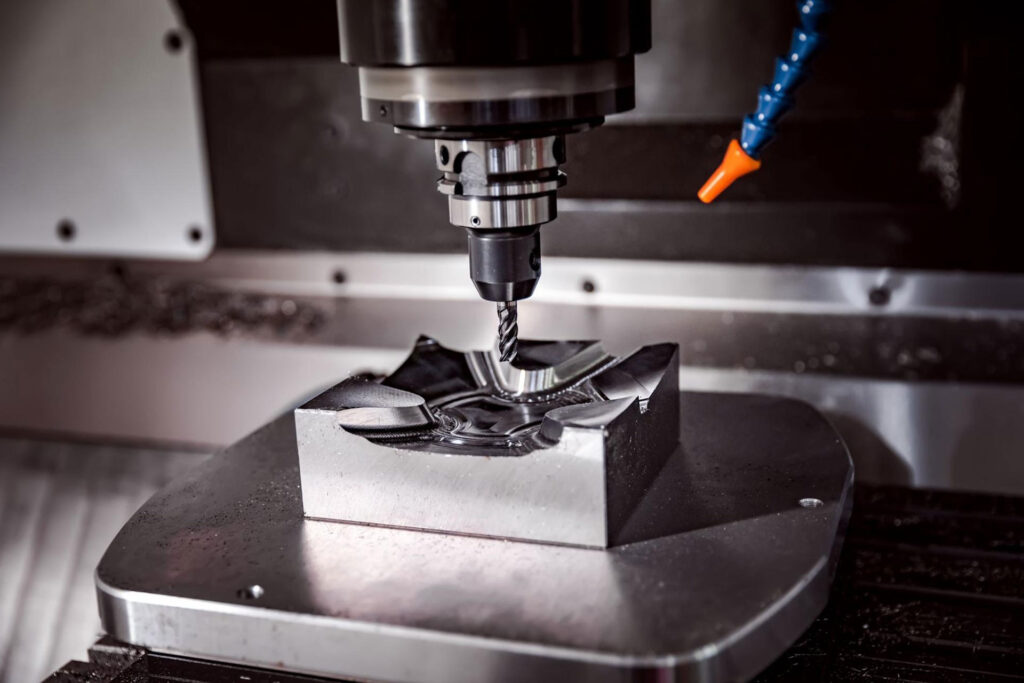
CNC (Computer Numerical Control) milling cuts material to create a finished design. The process involves multiple cutting tools controlled by a computer program that reads machine paths and translates them into instructions for each device. These machine paths originate from CAD/CAM software used to create a mechanical product design. For a better understanding, Computer Numerical Control (CNC) is a programming language that applies instructions to manufacturing machines. It can be used directly or indirectly to transform virtual objects into real ones. Milling is a process that involves the use of milling machines to cut or drill into materials. The name comes from the machine’s rotating cylindrical tools called cutting edges, which can vary in size and form—and are held within another tool (the spindle).
How Does CNC Milling Work?
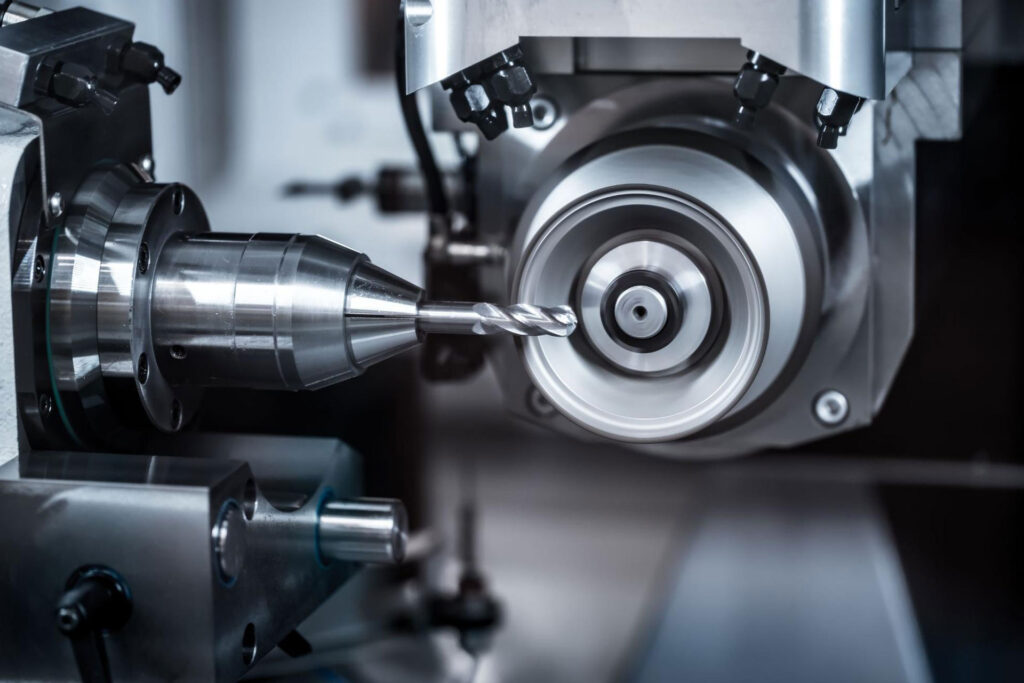
The CNC machining process begins when a design is inputted into a CAD program. The machine reads this file and processes the data in order to create parts from various materials with varying degrees of complexity — both 2D and 3D formats are possible. CAD (Computer-Aided Design) software then translates that design into a CNC (Computer Numerical Control) program, which tells the machine how to produce objects using materials with properties such as density and porosity.
Types of CNC Milling Machines
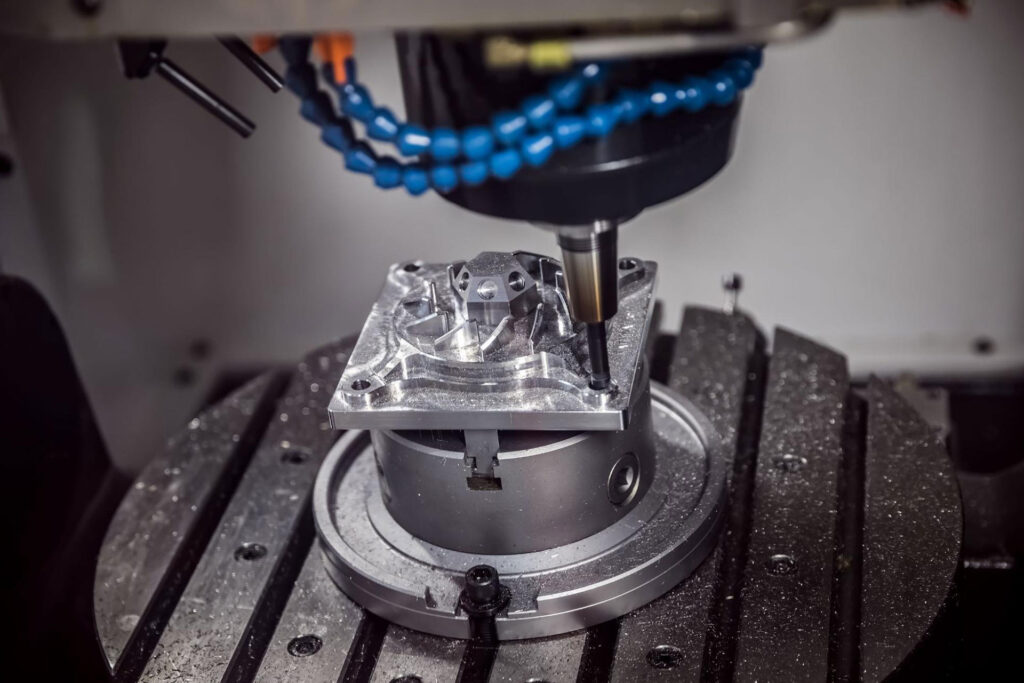
CNC milling machines are any milling machines controlled through a computer. However, there are several other types of machines, whether manual or CNC — that include axis classifications:
Vertical Milling:
A vertical milling machine uses a 3-axis milling table as its working surface, on which the spindle is mounted. In some cases (especially when using a horizontal “turret” head), the worktable can move along both X and Y axes; in these instances, however, typically, only one axis will be powered at any given time. The table moves only along the X-axis if a vertical bed mill is used. Using such a machine, the spindle travels along the arm’s length in the Y-axis direction.
Horizontal Milling:
In horizontal milling, the spindle moves horizontally rather than vertically, and many other components are similar to vertical milling. Horizontal mills generally perform better with heavier projects or longer ones. They are well suited with parts that require a lot of material to be removed because the swarf (the shavings created by cutting metal) falls away from the position and cutter.
Face Milling:
Face milling cutters, with teeth both on the periphery and front of the tool, are used for finishing applications. Face milling is also used to create flat surfaces and control the finished shape of a piece. Face milling can produce higher-quality finishes than other types of milling, and it works well with vertical and horizontal mills.
Plain Milling:
A plain milling cutter has teeth on its periphery that perform the cutting operation. In addition, narrow and wide blades are available, allowing deeper cuts and larger surface areas to be worked on. The coarse and fine-toothed cutters are used together, with slow cutting speeds for the rough edge and fast feed rates for the fine.
Angular Milling:
Angular milling is a milling operation in which the cutting tool’s axis of rotation is at an angle relative to the surface of the workpiece. As a result, single-angle milling cutters can produce more angular features, such as grooves or serrations — compared to their nonangled counterparts.
Form Milling:
Form milling is best used for irregular surface operations, such as cutting contours, outlines, or edges. It employs specialized cutters (concave ones and corner rounders) to achieve these results. In addition, hemispherical or semi-circular designs with complex parts would benefit from the form milling technique.
Why is CNC Milling Important?
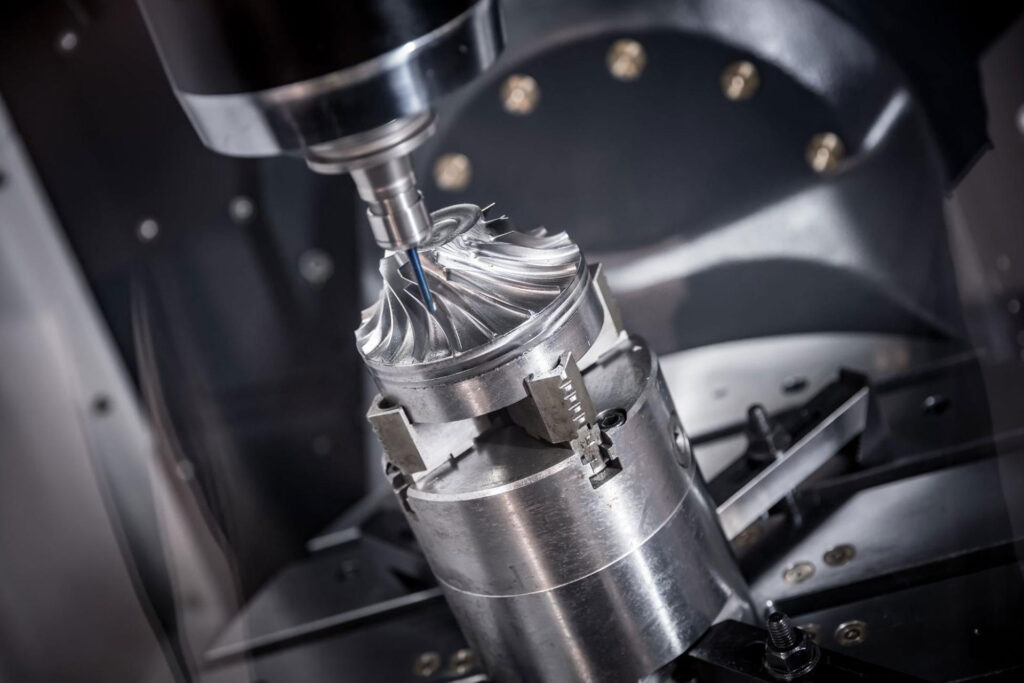
Digital technologies and CNC milling machines allow for the resolution of many problems which cannot be easily solved using prior methods. The technology approaches working processes in a more effective way (more solutions) and efficiently (using fewer resources). Without a CNC milling machine, cutting metal would be much riskier. But with the help of computer programs and access to high-definition designs, it is possible to create unique components that are extremely precise!
The more you know about CNC milling, the more likely you’ll be able to make good use of it in your future projects. Even if you’re not ready to purchase a milling machine, remember that there are plenty of other ways to get the benefits it can provide when part of a larger production workflow. This process lets you take a product from concept to fabrication faster than other manufacturing methods. It’s ideal if you need to create a prototype or if you can be flexible with the finished product. With the right tools and software, you’ll be able to make almost anything.
Do you want to learn more about CNC Milling? Contact us today to learn more about our products!