3D Printing in Construction: The Advantages and Disadvantages
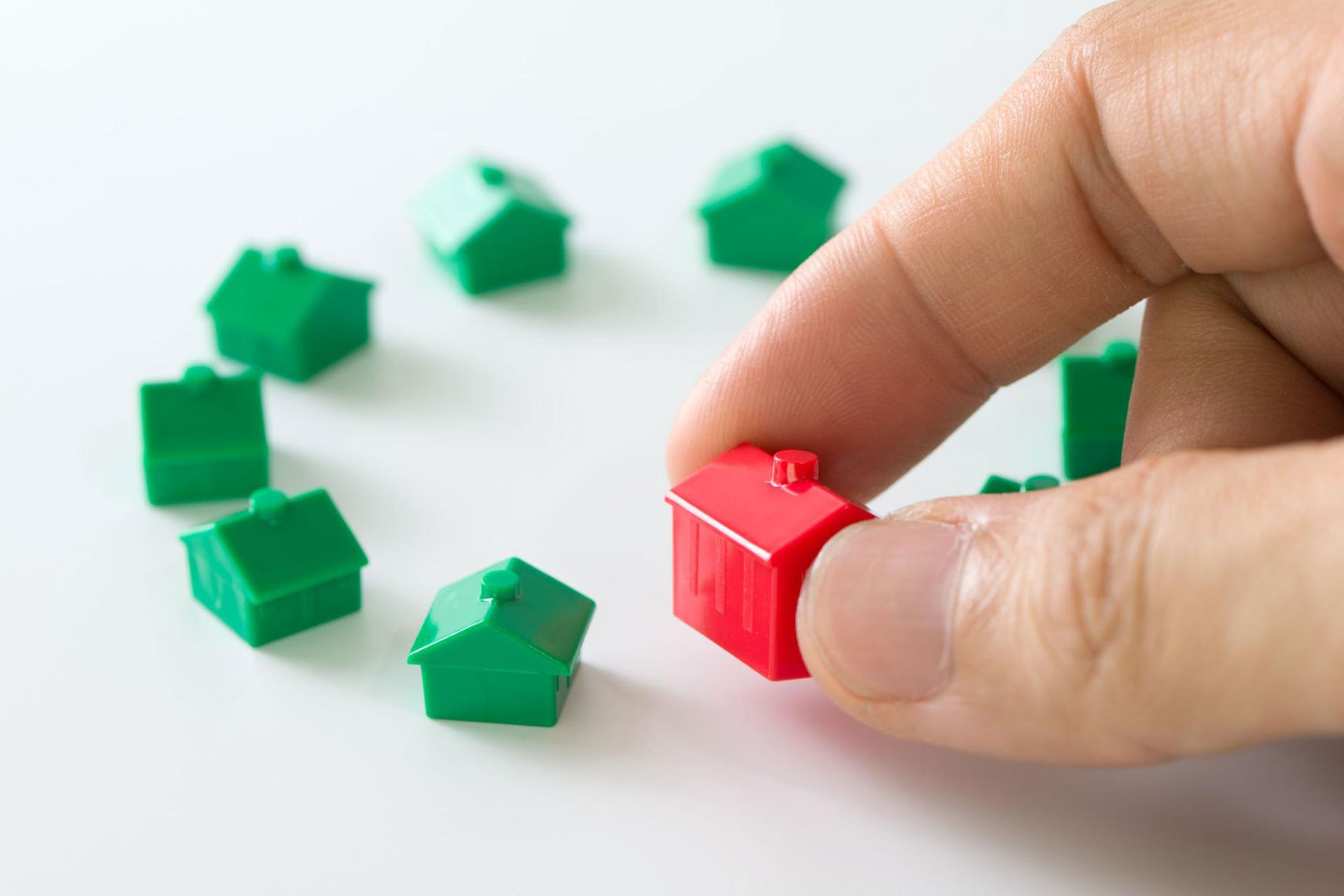
While there are many benefits to using 3D printing in the real estate industry, the technology is still new. There are still many challenges when it comes to building a 3D printed house. Some may even consider it a gimmick because it takes so much time and effort to produce these houses. However, industrial engineers believe that the 3D process will soon become the norm instead of the exception. That’s because those who are involved in this technology are currently facing a number of problems that are not insurmountable when you have today’s technology at your disposal.
Advantages:
1. Cost-Effective
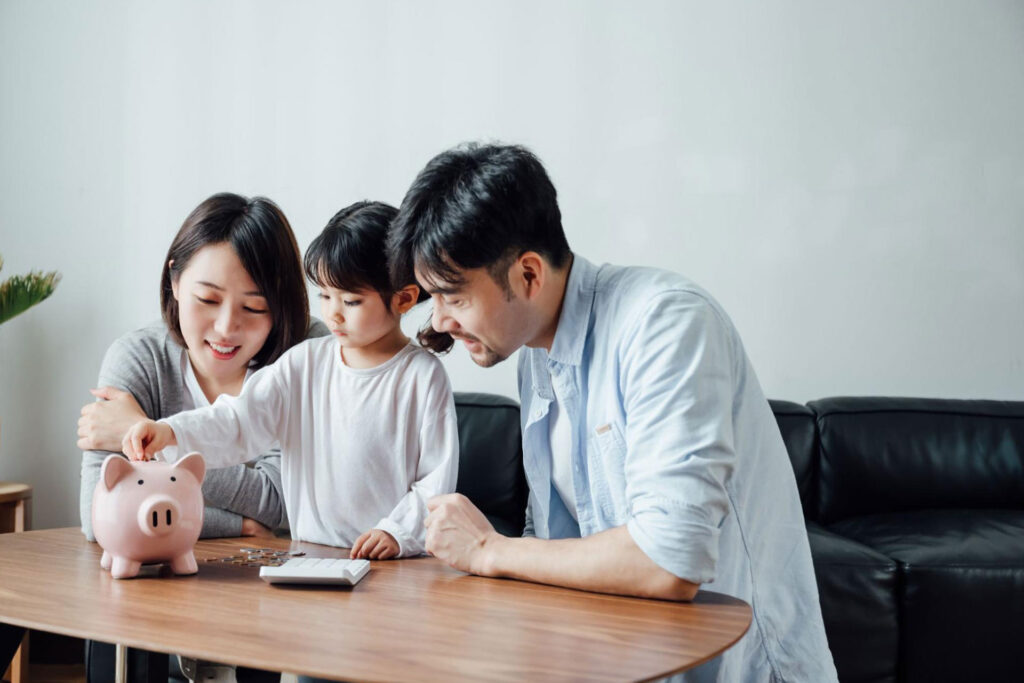
The biggest advantage of 3D printing in construction is its relatively affordable rate. When compared to traditional construction methods, 3D printing requires less time, manpower, and other resources. While traditional construction techniques always involve several men on the job site to complete the project — this is not the case with 3D printing. As a result, it eliminates the need for unskilled labor or skilled workers and thus, expenses like labor costs are considerably reduced over using conventional build methods. House building costs usually become a huge burden on the individual’s pocket. Plumbers, painters, carpenters, electricians, and other professionals have their own rates per hour which can cost you more than you expected. These professionals don’t completely make up for their professional fees but are just parts of your total construction expenses. 3D printing’s revolutionary technology is here to help lower your expenditures in these areas when constructing your home.
Related: The 5 Must-Know Benefits of 3D Printing
2. Saves A Lot of Construction Time
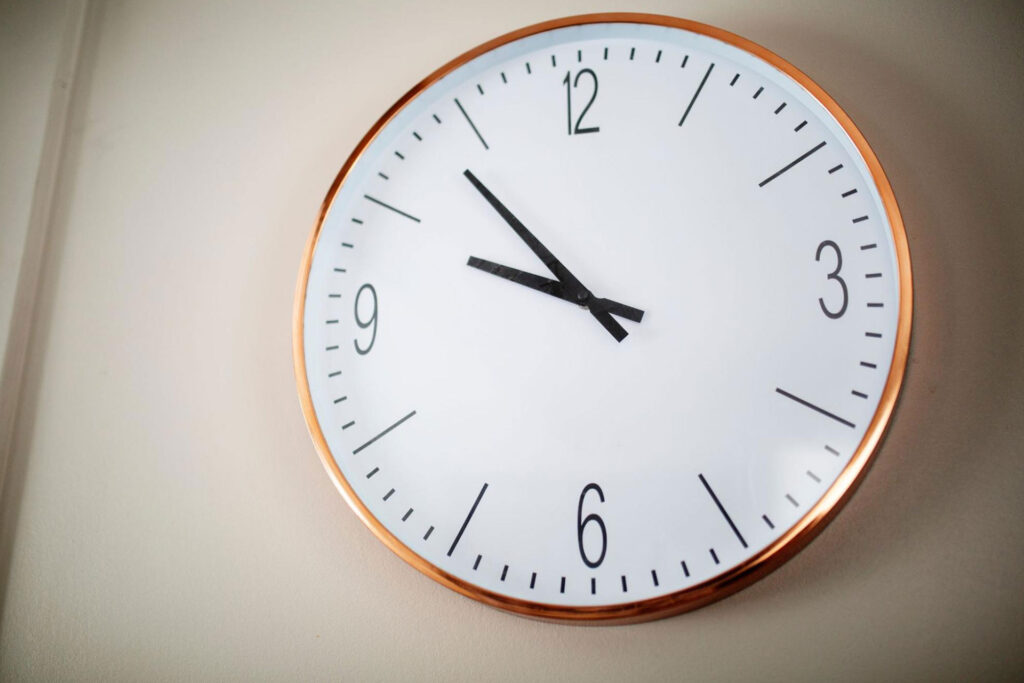
The use of 3D technologies in construction has a huge advantage over traditional construction. The use of this technology can drastically cut down the amount of time that is required to construct a building from months to just a few weeks sometimes. This can be especially useful in emergency situations where many structures need to be built quickly such as after earthquakes or some other type of disaster. 3D printing can build objects layer-by-layer out of plastic or other materials. It’s much faster than traditional construction methods and offers more customization in a more sustainable manner.
3. A Variety of Design Choices
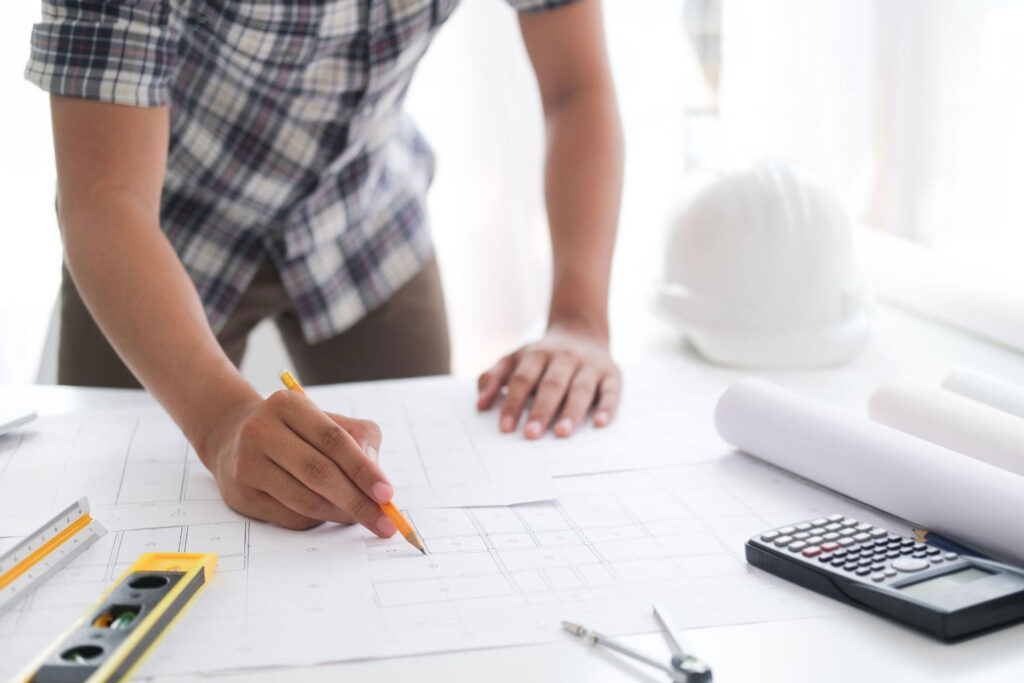
Since the late 1980’s, architects have discussed the possibility of building with concrete and especially printing concrete buildings possibly even from one printer. Today, these ideas are becoming low-cost realities. 3D printing is a big emerging technology that will radically transform the construction industry so it is no surprise to see a number of prominent construction companies beginning to explore this new capability. Recently, innovations in 3D printing have allowed concrete to be printed into complex shapes. This means designers can make new and exciting shapes. Structures made using 3D printing are sometimes referred to as “additive” because they are built up in layers.
Disadvantages:
1. Limited Materials
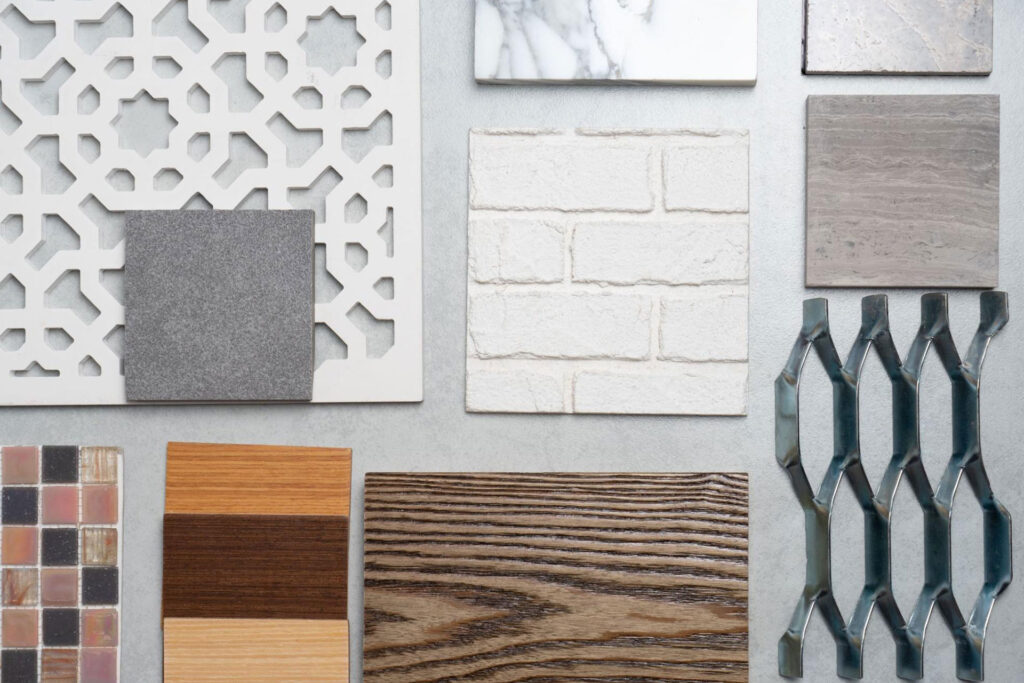
A lot of people don’t realize that there are already machines to print fully functional houses, but they are only limited to printing out a house’s concrete and plastic parts. Buildings which need wood beams and steel would not be able to use the 3D printer to complete those portions of the construction process.
2. Leaves A Negative Impact on Manpower
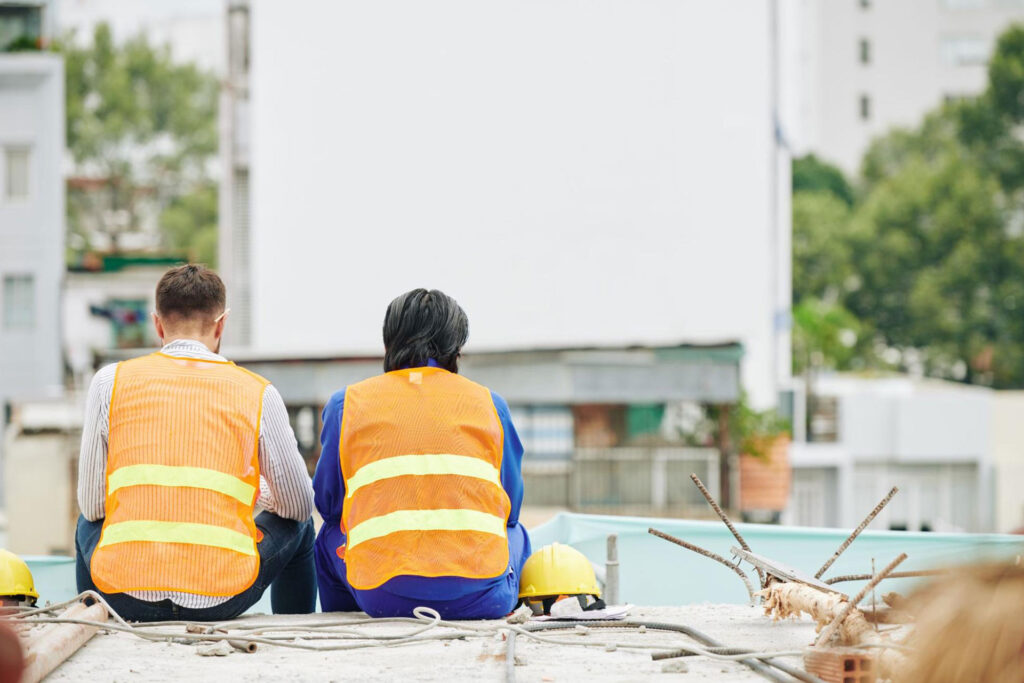
It’s been predicted that 3D printing technology will help make the building process faster, cheaper, and easier. But it won’t be the same for everyone; the simple construction workforce working around the world will have nowhere to go when they lose their jobs to automated machinery. It’ll mostly affect skilled manpower, as they’d have to learn how to use new technology to find employment if they choose to stay within that sphere of industry. Thousands of jobs will become redundant and millions of people will lose their source of income. Millions more may suffer from unemployment due to the lack of resources provided by conventional jobs, such as construction work. The problem can be averted to only a certain extent by workers shifting towards other work that is not automated or technology-based. But ultimately, automation is inevitable, and it’s starting with the construction industry.
The technology is still in its infancy and it will take some time before property developers can create 3D printed houses that are comparable to those produced on traditional building sites. When the time comes, we might see the construction industry going through some changes to adapt to this new technology.
Would you like to know more about 3D printed houses in the Philippines? Contact us today, we’d love to help you!