How to Choose the Right CNC Surface Grinder: 9 Top Tips
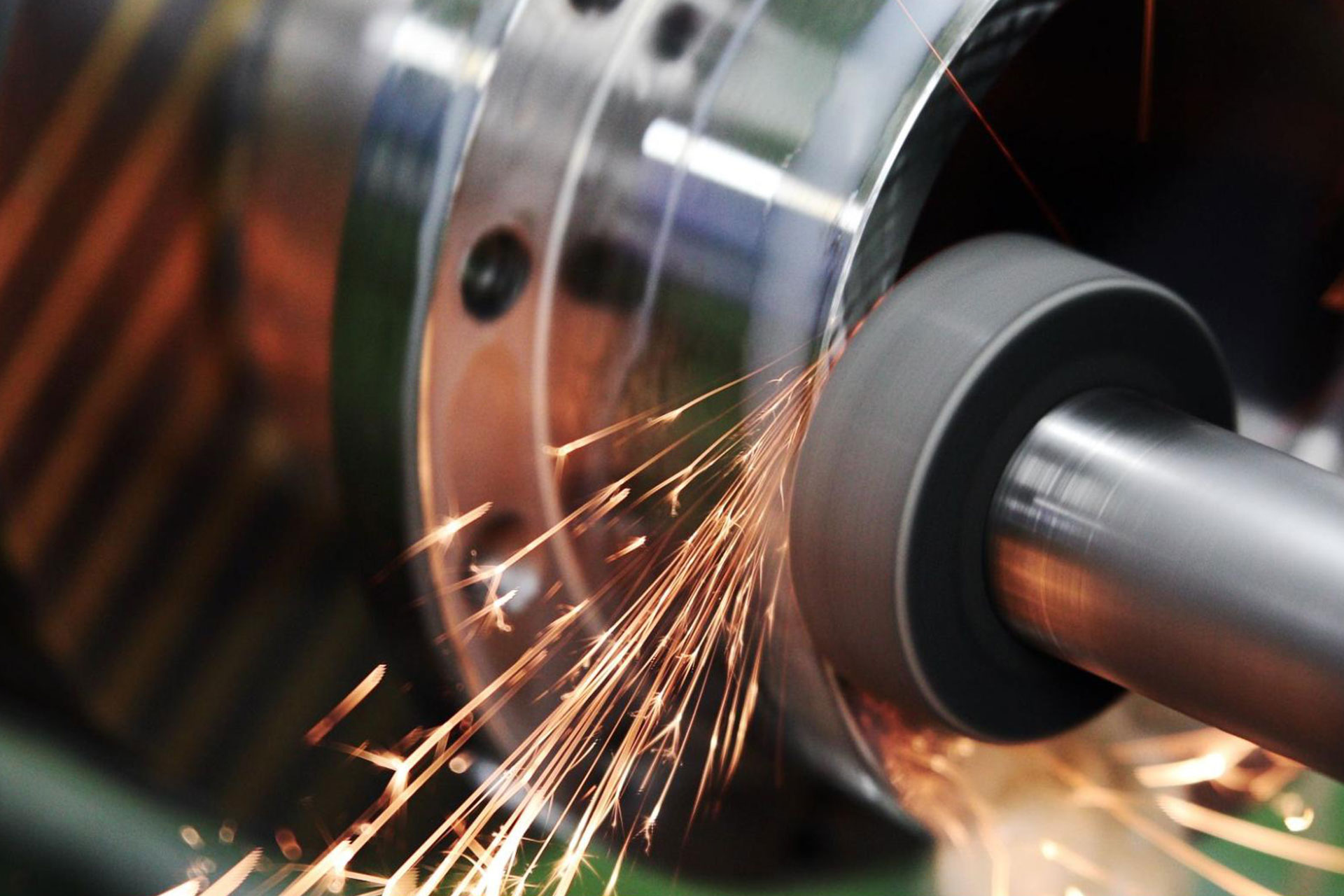
When it comes to precision machining, selecting the right CNC surface grinder is essential for achieving smooth, flat surfaces on metals and other materials. A high-quality CNC surface grinder brings accuracy, efficiency, and versatility, but with so many options, finding the best fit can be overwhelming. This guide offers top tips on choosing a CNC surface grinder that aligns with your needs, ensuring you make a well-informed decision.
Related: What is CNC Surface Grinding? An Easy Guide
On This Page
- Define Your Specific Grinding Needs
- Check Grinding Capacity and Table Size
- Choose the Right CNC Control System
- Evaluate Spindle Power and Speed Flexibility
- Consider the Accuracy and Tolerance Levels
- Review the Coolant and Lubrication Systems
- Prioritize Safety Features
- Assess the Total Cost and Long-Term Value
- Check Manufacturer Reputation and Customer Reviews
- Frequently Asked Questions (FAQs) About CNC Surface Grinder
1. Define Your Specific Grinding Needs
First, identify the specific applications you need the CNC surface grinder for:
- Material type: Consider the primary materials (steel, aluminum, or softer metals) you will work with. Certain grinders excel with specific materials.
- Size and shape of workpieces: The size of your workpieces will impact the grinding table size and axis movement.
- Precision requirements: If your projects demand tight tolerances, consider a CNC surface grinder with advanced accuracy features.
Tip: Make sure to tailor your choice based on the material and applications you handle most frequently.
2. Check Grinding Capacity and Table Size
Evaluating the grinding capacity enables the machine to accommodate your project’s dimensions.
- Table size: A larger table fits bigger workpieces but requires more space.
- X, Y, Z axis movement: See to it that the machine’s range of motion covers your specific project needs.
- Max grinding height and width: Check if the maximum grinding dimensions meet your requirements.
Tip: Look for a CNC grinder with a suitable grinding capacity and flexible settings to handle a variety of tasks.
3. Choose the Right CNC Control System
The control system is the brain of your CNC surface grinding machine. A user-friendly, reliable control system makes programming easier, enhancing productivity.
- Software compatibility: Verify if the CNC control system supports familiar or intuitive software.
- Ease of use: The simpler the interface, the faster you will master it.
- Automation features: Advanced CNC systems with automatic adjustment, monitoring, and calibration features help maintain consistent results.
Tip: If precision is essential for your projects, go for a CNC grinder with an advanced control system that ensures accuracy and efficiency.
4. Evaluate Spindle Power and Speed Flexibility
The spindle power and speed affect how efficiently and precisely the machine operates:
- Match power to material: For harder materials, choose a machine with higher horsepower.
- Adjustable speed settings: Flexibility in spindle speed is ideal for working with different materials and achieving varied finishes.
- Stability: A stable spindle with low vibration enhances the quality of the final product.
Tip: Selecting a high-power spindle with speed adjustability allows for versatility and high-quality grinding results.
5. Consider the Accuracy and Tolerance Levels
Precision is critical with CNC surface grinders, especially for industries like aerospace and medical manufacturing.
- Tolerance levels: Higher tolerance levels enable the grinder to meet strict specifications.
- Positioning accuracy: Accurate positioning helps maintain consistent precision.
- Feedback systems: Advanced grinders have real-time monitoring to adjust settings and maintain accuracy.
Tip: If your projects require a high level of precision, prioritize machines with advanced feedback systems and strict tolerance levels.
6. Review the Coolant and Lubrication Systems
High-speed grinding generates heat, which can impact the machine and product quality.
- Cooling the workpiece: Coolant systems prevent overheating and reduce thermal deformation.
- Extending machine lifespan: Proper lubrication reduces wear and tear on parts.
- Improving surface finish: Efficient cooling and lubrication contribute to a smooth, professional finish.
Tip: Look for a CNC surface grinder with a reliable coolant and lubrication system for better performance and machine durability.
7. Prioritize Safety Features
Safety is essential, especially when working with powerful machinery like CNC surface grinders. Make sure the grinder you choose has:
- Emergency stop buttons: Quick shutdown options for emergencies.
- Enclosures and guards: Protect operators from debris and accidental contact with moving parts.
- Real-time monitoring: Advanced grinders have sensors to detect abnormal vibration or temperature changes.
Tip: A grinder with robust safety features minimizes risks and protects both operators and equipment.
8. Assess the Total Cost and Long-Term Value
Cost goes beyond the initial purchase. Consider maintenance, repairs, replacement parts, and software updates.
- Budget wisely: Find a machine that meets your needs without compromising on essential features.
- Long-term durability: Investing in a quality machine often pays off in the long run.
- After-sales support: Choose a manufacturer known for responsive customer support and easily accessible replacement parts.
Tip: Balancing cost with the machine’s long-term value and features allows you to get the best CNC surface grinder for your budget.
9. Check Manufacturer Reputation and Customer Reviews
A reputable manufacturer is a solid indicator of a reliable machine. Research brands known for quality, support, and durability.
- Brand reputation: Look for manufacturers with strong reputations for customer support and product reliability.
- User reviews: Customer reviews provide real-life insights into performance and potential issues.
- Warranty: A comprehensive warranty reflects confidence in the product’s quality.
Tip: A reputable manufacturer offers not only a reliable machine but also a dependable support network for ongoing needs.
Frequently Asked Questions (FAQs) About CNC Surface Grinder
1. What are the key features to look for in a CNC surface grinder?
Key features include grinding capacity, control system compatibility, spindle power, tolerance levels, coolant and lubrication systems, and safety features.
2. How do I determine the right spindle power for my CNC surface grinder?
Choose spindle power based on the hardness of the materials you work with. Harder materials typically require higher horsepower.
3. What industries benefit most from CNC surface grinders?
Industries requiring high precision and surface quality—such as aerospace, automotive, and medical device manufacturing—benefit greatly from CNC surface grinders.
4. Are CNC surface grinders more accurate than manual grinders?
Yes, CNC grinders are typically more accurate and consistent due to automated control, reducing human error.
5. How do I maintain a CNC surface grinder for longevity?
Regular maintenance, including proper lubrication and coolant checks, is essential. Follow the manufacturer’s guidelines for routine servicing.
Choosing the right CNC surface grinder can enhance productivity, precision, and versatility in your workshop. If you’re a beginner, an experienced professional in the manufacturing industry, or simply looking to explore CNC technology, joining a Fab Lab in the Philippines can also be a great way to gain hands-on experience. With careful consideration of factors like grinding capacity, control systems, spindle power, and tolerance levels, you can select a machine that perfectly suits your needs. To top it off, investing in a high-quality CNC surface grinder from a reputable manufacturer can set your business up for long-term success.
Looking for quality CNC Surface Grinding in the Philippines? Contact us today to know more about our products!